The installation experience of wheat flour mill machine
Category : Africa Hongdefa Machinery wheat mill wheat milling process
Wheat Flour mill machinery, there is many machines and between the machine have connection. In order to improve work efficiency, improve the quality of the project, carefully read the drawings before installation, inspection site, in order to determine the better construction program. The operation of the process to fully integrate the actual situation on the scene, rather than blindly according to the design drawings for cutting and equipment layout. At the same time, construction must pay attention to the safety of personnel and equipment.
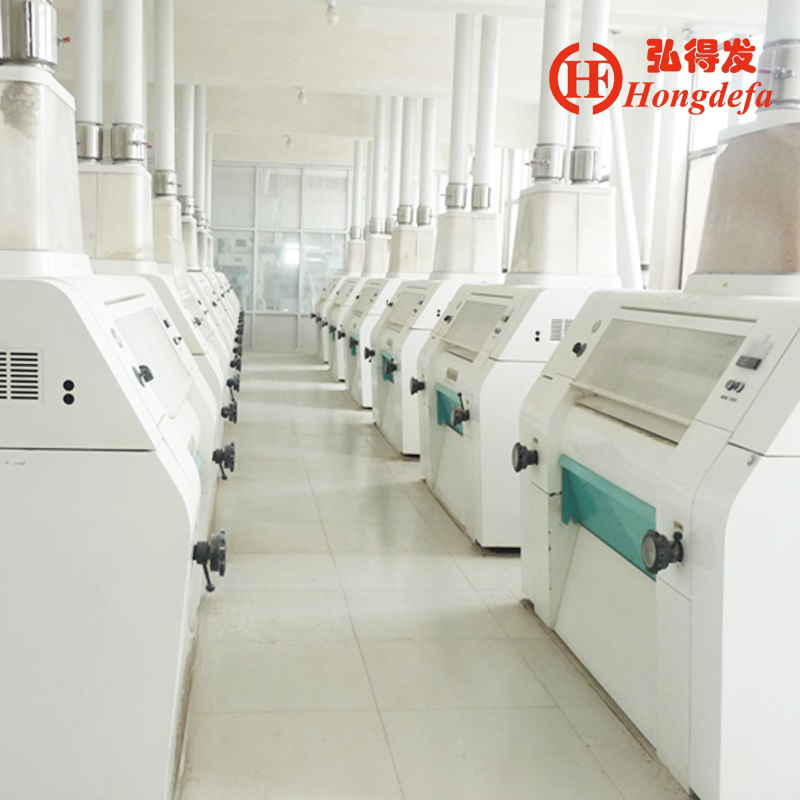
National Development and Reform Commission, Ministry of Industry and Information Technology released the “food industry” second five “development plan” is expected by 2015 to deal with wheat 400t / d above the proportion of enterprises will increase to more than 65% Increase by 15 percentage points, the author of these years involved in the installation and commissioning of the flour mill single line of the daily processing capacity has reached a minimum of 400t / d, and at least two production lines at the same time boot. This trend of development to the flour equipment installation industry has brought great opportunities for development, but also to the installation work put forward higher requirements, bringing greater challenges.
Get price and more details
1.Flour equipment installation requirements and the difficulty
The quality of the installation project not only to meet the national and industry standards, such as: GB50300-2013 “construction quality acceptance of a unified standard”, GB 50231-2009 “mechanical equipment installation and acceptance of the general norms”, but also to meet the construction The special requirements of the unit. In ensuring the use of functions, operation and inspection and maintenance of the premise, the enterprise will be on the overall external appearance of the demanding requirements. We may one-sidedly believe that the installation of equipment is nothing more than in accordance with the layout of the main map, auxiliary equipment in place fixed, according to profile, elevation to determine the direction and elevation of the pipeline can be. In fact, not yet, because there is no specific food machine equipment for the installation of standards and norms, the installation process a lot of practices are drawing on the experience of other projects to operate. This requires practitioners with a wealth of experience in installation and commissioning. In addition, because the flour mill of each device is not isolated, and its front and rear, up and down, are related to the equipment with the match, which requires the installation staff to have a global view, before proceeding to establish the overall idea of installation, Clear the connection between the equipment, must not blindly start. Flour mill installation difficulty is mainly concentrated in the following two aspects: First, the process is complex, many channels. Modern milling process to promote light grinding subdivision, strengthen the classification, especially the high-sieve outlet between the powder pipe, with “so much” to describe it is not too much, but also with a lot of tee and fighting, the pipeline not only Easy to get wrong, and there may be between the pipeline space conflict. Another major reason is that the flour mill pipeline has the installation angle requirements. As the flour mill raw materials, finished products, finished products and by-products have their own self-slip angle (wheat 27 ~ 31 °, milling intermediate 37 ~ 44 °, standard powder 40 ~ 44 °, bran 37 ~ 40 °) , Therefore, the first task of pipeline installation is to ensure that the material can be smooth in which circulation, followed by consideration of beauty.
- Examples of flour mill equipment installation
1) Output screw under the bin of clean section
Construction drawings tend to mark the installation height of the conveyor and the installation location, which are understandable, but also a complete design drawings indispensable. However, the installation staff may be based on profile, elevation drawings made in advance of the size of the conveyor belt, while ignoring the actual situation of the scene. The size of the drawings is an ideal condition, but the construction of the building will inevitably produce some changes (floor thickness error, the bottom of the ground elevation error, etc.), and sometimes even a more substantial change, so as to give Subsequent equipment installation work is difficult. In order to prevent the material from flowing out of the automatic classification phenomenon, clean up the wheat warehouse is often designed as a multi-export form, all the export of the slip pipe pool to a bucket and then by the wheat into the screw conveyor, so the top of the conveyor to leave enough Height is used to install the collection bucket and with wheat, but the conveyor can not be installed too low, because it also down the hoisting machine feeding. So the conveyor height of the conveyor to meet the wheat from the slip angle of the premise can be installed as low as possible in order to collect the bucket and with the wheat to leave enough space, but also to facilitate the daily management and maintenance, and unnecessary According to the height of the drawings marked to the production and installation.
Get price and more details
2) Input conveyor at the top of the bin installation
General roof are open-air, reserved holes can not be arbitrarily changed, changes may lead to the warehouse into the water, resulting in mildew of grain. On the other hand, the current capacity of the vertical silo are in the direction of large-scale development, is often tens of thousands of tons of capacity, due to the large number of target storage, transport distance is longer, scraper scraper is often arranged in sections, by The former scraper back to a feeding, the same scraper material may be able to enter two rows or even more positions. In order to save the material, the scraper is often tilted, the inlet is low and the outlet is high, and each outlet has a slip tube and a pneumatic gate. The above technical requirements and characteristics of the scraper machine to fully determine the minimum installation height, below the minimum installation height to ensure that the wheat from the slip angle. Therefore, in determining the installation height of the scraper must be in advance to understand the actual situation at the scene (reserved hole position is correct, scraper material to enter the target, etc.), rather than blindly according to profile, elevation On the size of the production scale, if the civil construction process errors or errors may cause the actual installation height changes, rework time is a waste of material and labor-intensive.
3)Some machine installation Precautions
As the structure of the device itself and the working principle, the installation, one can not damage its vulnerable parts, two to ensure that its normal, stable work required for the basic conditions. Some precision equipment, such as measuring scales, gravity meters, balers, water control, etc., these devices are equipped with a sensing device, in the installation to avoid strong electric field, magnetic field and high temperature environment, welding or gas cutting Should pay attention to protection. In addition, the installation must be adjusted to a good level, installed firmly to avoid shaking to ensure its measurement accuracy, the equipment bracket or base to be self-contained, can not be shared with other stents or connected In order to ensure the accuracy of the sensor operation, such equipment requirements upstream The flow rate is stable, so the upper end of the general requirements are required to install the buffer bucket or buffer elbow to reduce the impact of incoming to ensure the stability of the flow. Take the water controller as an example
Bucket elevator →hopper →Level indicator→ level high/low → No work ↓ Micro process unit
↓ Down-hopper Pneumatic valves ← The electromagnetic valve←compress air
The traditional process of wheat and wheat are out of the “one clean” treatment by the hoist to the top, then enter the water control device to detect the real-time flow of wheat and the initial moisture content, the controller and then set the target Moisture content to determine the water machine water. From the control device to detect changes in the flow of wheat to indicate the change in the amount of water to change the amount of water will be less time, if the flow of incoming instability will lead to water is not accurate and thus affect the grinding and grinding effect. In addition, the water control device to detect the initial moisture content of wheat requires the hopper in the wheat level to maintain a certain height so that the detection probe can be detected, if the material is too high or too low, the hopper below the gate will be corresponding Adjust the opening degree of their
own in order to maintain the level of wheat in the hopper, if the upstream flow of the incoming flow can not be maintained at a stable level, then the gate opening degree will change frequently, the gate opening degree changes first identified by the probe Information feedback to the micro-red space may cause the hoisting machine blocking material, causing the system to stop. Such as the details are easy to be ignored, the drawings are also very difficult to fully express it, which gives managers and the quality of the installation staff made a high demand.
- Safety when installation
The last and most important is the safety of the installation process, including personal and device safety. Welding, gas cutting should pay attention to the work below the staff and equipment, personnel leave the time to cut off the power and gas source, after get off work to arrange full-time staff to inspect. Personal safety is the most important, even if the
installation of the perfect flaw, if there is a security incident will be a vote veto. Especially in the early installation, equipment and pipelines are not in place, more holes reserved, be sure to do a good job of holes and edge protection and warning work, at the same time to strengthen the training, the construction workers to carry out safety education, improve its Own security awareness.
4 Total
Flour milling machine installation requires practitioners with a global view and clear ideas, according to the actual situation of the scene to adjust the construction of the program flexibility, and not mechanically according to the design drawings for equipment and pipe connections. Under the basic premise to meet the functional realization, we should strive to make the equipment layout reasonable, the pipeline to the beautiful. Problems that are not found and resolved during the installation process are exposed during commissioning, especially when commissioning is carried out. Due to the material when the pipe material, this time the changes will cost more time and effort, so the installation must be taken seriously, to find and solve the problem, as far as possible in the installation to be handled, must not be opportunistic, only so When debugging can be done confidently, leisurely.
Get price and more details
If you any questions about wheat flour mill machine, contact me with:
Cell/WhatsApp/: +8613833461840
Email: maizewheatmill@gmail.com
Or click www.maizewheatmill.org to visit our website
Thanks!
Vanisa
近期评论